Conventional Castable Manufacturers
The composition of a conventional castable typically consists of refractory aggregates, binders, and additives. Refractory aggregates are heat-resistant materials like alumina, silica, and various minerals, which provide the castable with its thermal resistance.Binders are used to hold the aggregates together, and they are often composed of cement, clay, or other bonding agents.
Additives may be included to enhance specific properties such as workability, setting time, and resistance to thermal shock. One of the key advantages of conventional castables is their versatility and ease of installation.
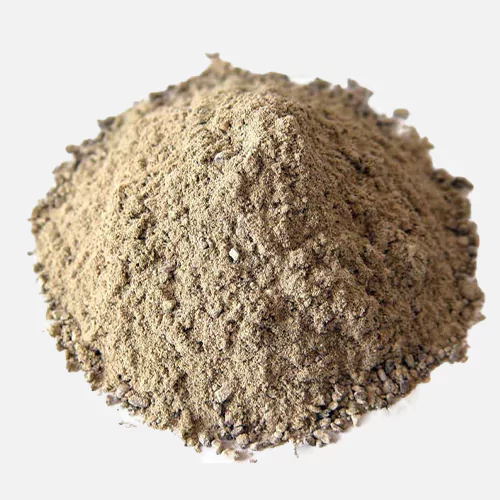
Conventional Castable Suppliers
Selection of Raw Materials: The primary raw materials used in conventional castables are aggregates, binders, additives, and water. Aggregates are granular materials that provide the bulk of the structure and properties to the castable. Common aggregates include high-alumina, mullite, andalusite, silicon carbide, and others. Binders are used to hold the aggregates together after drying and firing. Additives are included to enhance specific properties like flow, workability, and strength.
Batching and Mixing: The raw materials are accurately weighed according to the desired formulation. The aggregates are mixed with binders and additives in a proper ratio to achieve the desired properties of the castable. The mixing process ensures even distribution of the components to achieve a uniform material.
Addition of Water: Water is added to the dry mix to create a wet, workable material. The amount of water added needs to be carefully controlled to achieve the desired consistency and flowability without compromising the final properties.
Benefits of Our Products :
- Exceptional Quality
- Innovative Design
- Reliability and Durability
- Cost Efficiency
In summary, our products stand out due to their exceptional quality, innovative design, reliability, customization options, cost efficiency, expert support, sustainability, proven track record, and commitment to continuous improvement.
Where It Is Used?
- Power Generation
- Heat Treatment Furnaces
- Petrochemical Industry
- Kiln Lining
- Boiler Refractory Lining
- Incinerators