Best High Alumina Refractory Bricks Manufacturers in India
High Alumina Refractory Bricks are special bricks with more than 50% alumina content. They’re made from baked bauxite or materials rich in alumina. What makes them stand out is their ability to handle really high temperatures, from 1200°C to 1700°C. That’s much hotter than regular fire bricks, making them perfect for tough spots in boilers, kilns, and furnaces.
We’re proud to be one of the top makers of these bricks in India. Whether it’s high alumina fire bricks, refractory bricks, boiler bricks, blocks, or furnace bricks, we’ve got it covered. Our focus is on providing reliable and long-lasting solutions for demanding situations.
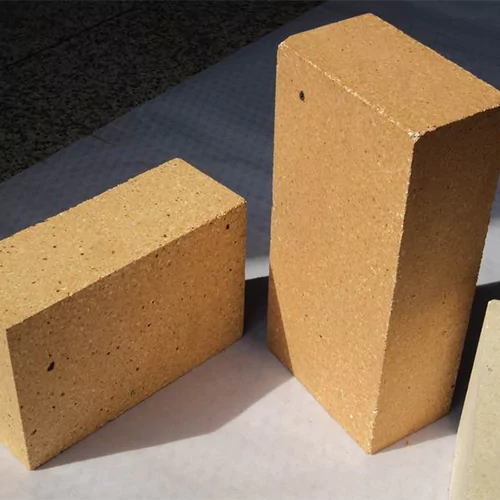
Your Source for High Alumina Refractory Bricks in India
The manufacturing process of high alumina refractory bricks involves several critical steps to create a material capable of withstanding extreme temperatures and harsh environments. The process begins with the selection of high-purity raw materials, primarily consisting of alumina-rich sources. These sources could include bauxite, corundum, or synthetic alumina powders, chosen for their high alumina content and minimal impurities.
- Raw material selection: The first step is to select the raw materials. The most common raw materials used for high alumina refractory bricks are bauxite, diaspore, and kyanite. These materials are all high in alumina content, which is essential for the high refractoriness of the finished bricks.
- Calcination: The raw materials are then calcined, which is a process of heating them to a high temperature in order to drive off moisture and volatile impurities. This step is important for improving the strength and durability of the finished bricks.
- Mixing: The calcined raw materials are then mixed with other ingredients, such as binders, fluxes, and additives. The binders help to hold the bricks together, while the fluxes help to lower the melting point of the bricks. The additives can be used to improve the properties of the bricks, such as their refractoriness, thermal shock resistance, or chemical resistance.
- Forming: The mixed ingredients are then formed into the desired shape of the bricks. This can be done by a variety of methods, such as dry pressing, wet pressing, or isostatic pressing.
- Drying: The formed bricks are then dried to remove any remaining moisture. This step is important for preventing the bricks from cracking during firing.
- Firing: The dried bricks are then fired at a high temperature in a kiln. This step is the most important step in the manufacturing process, as it is during this step that the bricks develop their high refractoriness and other properties.
- Cooling: The fired bricks are then cooled slowly to prevent them from cracking.
the manufacturing process of high alumina refractory bricks involves selecting pure raw materials, blending them to achieve desired properties, shaping the mixture into bricks, and subjecting them to high-temperature firing. This intricate process results in the creation of durable, heat-resistant bricks essential for applications in industries where extreme temperatures and harsh conditions are prevalent.
Advantages of High Alumina Bricks
- High Heat Resistance
- Thermal Insulation
- Chemical Resistance
- Improved performance
- Extended lifespan
Where you can use Alumina Refractory Bricks
Fire brick is mostly used where heat insulation is required. For example,in :
- Food Industries
- Steel Industries
- Glass Industries
- Furnaces
- Machine manufacturing units