Chrome Magnesite Bricks Manufacturers
Chrome magnesite bricks are specialized refractory materials that play a crucial role in high-temperature industrial applications. These bricks are designed to withstand the extreme heat and corrosive environments found in various industrial processes.
They are composed of a mixture of magnesia and chromite , which imparts unique properties to the bricks.One of the key advantages of chrome magnesite bricks is their exceptional resistance to high temperatures.
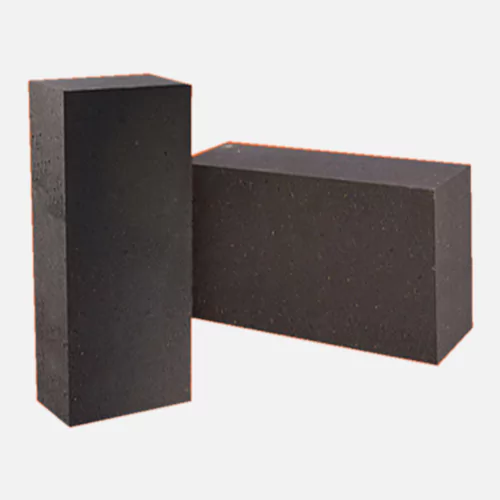
Chrome Magnesite Bricks Suppliers
- Preparation of raw materials: The raw materials used for making chrome magnesite bricks are magnesite ore, chrome ore, and a bonding agent. The magnesite ore should be high in magnesium oxide (MgO) content, while the chrome ore should be high in chromium oxide (Cr2O3) content. The bonding agent is typically a clay or a resin.
- Mixing: The raw materials are mixed together in a pug mill or a mixer to form a homogeneous mixture. The mixing process is important to ensure that the ingredients are evenly distributed and that the bonding agent is properly dispersed.
- Pressing: The mixed material is then pressed into molds to form the desired shape of the brick. The pressing pressure is typically high, in the range of 100 to 200 MPa, to ensure that the brick is dense and strong.
- Drying: The pressed bricks are then dried to remove any moisture. The drying process is typically carried out in an oven at a temperature of 100 to 200 degrees Celsius.
- Sintering: The dried bricks are then sintered in a furnace at a high temperature, typically in the range of 1600 to 1800 degrees Celsius. The sintering process causes the bricks to harden and to become chemically and physically stable.
Features of Chrome Magnesite Bricks :
- Refractoriness
- Dimensional Stability
- Chemical Inertness
- Application Versatility
- Insulating Properties
- Tailored Formulations
Process of Making Chrome Magnesite Bricks :
The main raw materials used in chrome magnesite brick production are magnesia (magnesium oxide, MgO) and chromite (iron chromium oxide, FeCr2O4). These materials are typically obtained from mining or other sources. The magnesia is usually high-purity, dead-burned magnesia to ensure high refractoriness and stability. The chromite provides resistance to corrosion and contributes to the refractory properties.
The magnesia and chromite are carefully proportioned based on the desired properties of the final product. Other additives, such as bonding agents, plasticizers, and stabilizers, might also be added to improve workability, plasticity, and sintering behavior.
Advantages Of Our Products :
- Long Service Life
- Versatility
- Customizability
- Chemical Inertness
- Abrasion Resistance
- Refractoriness
- Mechanical Strength
Where It Is Used?
- Refining Industry
- Incineration Plants
- Chemical Industry
- Petrochemical Industry
- Cement Industry