Ramming Mass for Continuous Casting Manufacturers in India
Jindal Refractories holds as being a leading brand in the world of refractory solutions, and our Ramming Mass is a excellent example of our resolve for excellence. Especially formulated for induction furnaces, our Ramming Mass consists of a powder produced by deceased, burned magnesite. Incorporating particular chemicals boosts its attributes, making it a superior option for various business programs. Being a well known Ramming Mass Manufacturer based in India, we be proud of providing merchandise characterized by purity and high overall performance.
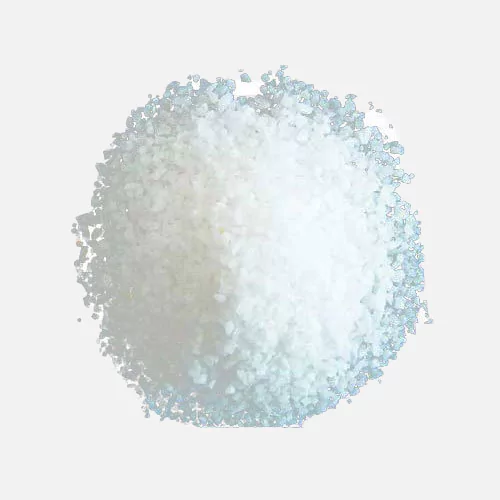
Mainly found in the coating of induction furnaces, our Ramming Mass takes on a critical role in impacting on heating overall performance. The standard of this important part directly affects not simply the furnace’s functional productivity but also the metallurgical manage in iron and stainlesss steel production. At Jindal Refractories, we modify our Ramming Mass to accommodate the furnace’s make and ability, guaranteeing a specific formula of granules without any steel.
What units our Ramming Mass apart is its outstanding wholesomeness, great effectiveness against corrosion, and outstanding energy stableness. In contrast to opponents, our merchandise contains considerably less clay, binders, and humidity, bringing about improved resistance to spalling and abrasion. Customers value the reliability and productivity our Ramming Mass produces in their business operations.
Getting among the largest Ramming Mass Manufacturers in India, we expand our achieve to international trading markets, exporting to Saudi Arabia, Indonesia, UAE, Tanzania, Sudan, United states of america, and Turkey. Our diversified range of Ramming Mass grades caters to the specific needs of consumers across diverse businesses.
Whether or not you’re trying to find a Ramming Mass Supplier in Rajasthan, Jaipur, or anywhere in India, Jindal Refractories holds when your respected lover. Our commitment to quality, accuracy, and consumer satisfaction causes us to be an ideal selection from the refractory market. Elevate your business operations with Jindal Refractories’ top-notch Ramming Mass solutions.
Ramming Mass for Continuous Casting Suppliers in India
- Raw material selection: The first step is to select the raw materials for the ramming mass. The type of raw materials will depend on the desired properties of the ramming mass. For example, alumina, silica, and magnesia are often used for ramming mass because they are refractory materials with high melting points, good thermal conductivity, and resistance to thermal shock.
- Mixing: The raw materials are then mixed together in a pug mill. The pug mill is a machine that mixes the materials together and kneads them until they are evenly distributed.
- Forming: The mixed materials are then formed into the desired shape. This can be done by hand, by using a machine, or by a combination of both.
- Drying: The formed ramming mass is then dried to remove any moisture. This is important because moisture can reduce the strength and durability of the ramming mass.
Ramming mass is a type of refractory material that is used in the continuous casting of metals. It is made from a mixture of refractory materials, such as alumina, silica, and magnesia, and binders, such as clay and water.
Ramming mass is used to create a dense, monolithic lining that can withstand the high temperatures and corrosive environments found in the continuous casting process. It is also used to create a smooth surface that can help to prevent molten metal from sticking to the lining. Ramming mass is typically applied by hand, using a hammer or ram.
Jindal Refractories is the best Ramming Mass Manufacturer and Supplier in Rajasthan, Jaipur and in all over the India.
Advantages Of Our Ramming Mass:
- High melting point
- Good thermal conductivity
- Resistance to thermal shock
- Chemical inertness
- Durability
- Easy to apply
Where Ramming Mass Is Used?
- In the tundish
- In the mold
- In the chill block
- In other parts of the continuous casting machine