Submerged Entry Nozzle for Continuous Casting Manufacturers
The primary function of the SEN is to regulate the flow of molten metal into the mold, controlling factors such as flow rate and turbulence. This control is essential for achieving consistent casting results and producing high-quality steel products. The design of the SEN can influence the overall efficiency of the continuous casting process, as well as the quality and surface finish of the final product.
To maintain effective operation, the SEN must be well-maintained and periodically replaced, as it can be subjected to wear and erosion due to the harsh conditions it experiences.
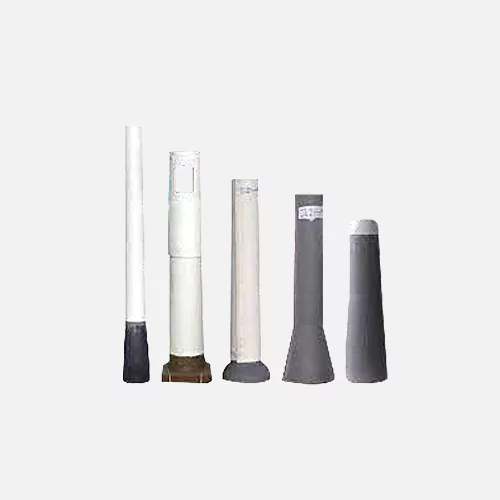
Submerged Entry Nozzle for Continuous Casting Suppliers
The first step is selecting the appropriate refractory material or ceramic for the SEN. These materials are chosen for their ability to resist high temperatures and chemical reactions with the molten metal. Common materials include alumina, zirconia, magnesia, and various combinations of these.
After firing, the SEN might undergo further machining and shaping to achieve its final dimensions and smooth surfaces. Precision machining ensures that the nozzle meets the required specifications for flow control and durability.
Depending on the specific design, the SEN might be integrated with other components before being installed in the continuous casting system. These components can include shrouds and other flow control devices.
Advantages Of Our Products :
- Improved Flow Control
- Reduced Inclusions and Defects
- Enhanced Productivity
- Uniform Solidification
- Minimized Air and Oxide Entrainment
- Easier Process Monitoring
Where It Is Used?
- Aluminum Casting
- Copper and Copper Alloys
- Other Metal Alloys
- Precise Alloy Control
- Product Diversification
- Increased Casting Speed