Slide Gate Plates for Continuous Casting Manufacturers
The slide gate plate consists of several key elements, including the plate body, nozzle, and slide mechanism. The plate body forms the main structure, providing stability and resistance to the harsh environment. The nozzle, an essential part of the plate, serves as the outlet through which the molten material flows. Precise design and positioning of the nozzle are critical to achieving accurate control over the material’s flow rate.
A notable feature of the slide gate plate is its slide mechanism, which allows for the adjustment of the nozzle’s opening.
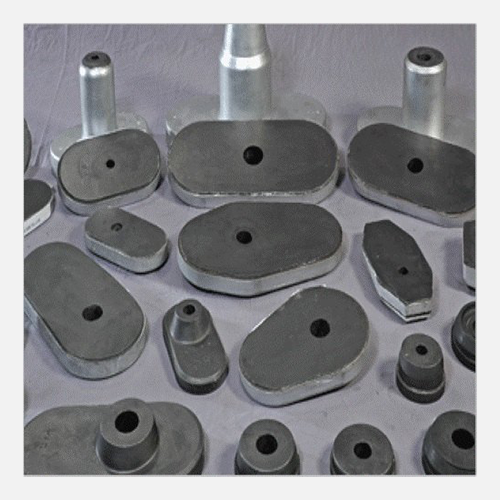
Slide Gate Plates for Continuous Casting Suppliers
The prepared refractory mixture is shaped into the desired plate body using methods such as casting, pressing, or extrusion. Casting involves pouring the mixture into molds to create the plate’s initial form. Pressing involves compacting the mixture under high pressure to achieve the desired shape, and extrusion involves forcing the material through a die to create a continuous profile.
The formed plate bodies are air-dried or heated in controlled environments to remove any remaining moisture. This step is crucial to prevent cracking or defects during the subsequent firing process.
The dried plate bodies are fired in kilns at extremely high temperatures, typically exceeding 1000°C (1832°F). This firing process, known as sintering, causes the refractory materials to chemically bond and transform into a solid, dense structure with the desired physical properties.
Advantages Of Our Products :
- Precise Flow Control
- Reduced Material Waste
- Minimized Contamination
- Enhanced Process Efficiency
- Extended Service Life
- Cost Savings
Where It Is Used?
- Refractory Material Production
- Metallurgical Research
- Heat Treatment Processes
- Molten Slag Handling
- Chemical Industry
- Automotive and Aerospace
- Steelmaking