Well Block for Bottom Pouring Set Manufacturers
A well block is a type of concrete well block that is poured from the bottom up. This type of well block is typically used in deep wells, as it allows for a more uniform concrete pour and reduces the risk of voids and cracks. Bottom pouring set well blocks are made of a mixture of cement, sand, and water. The concrete is poured into the bottom of the well casing and allowed to set.
Once the concrete has set, the next course of blocks can be added. This process is repeated until the well is complete.Bottom pouring set well blocks offer a number of advantages over other types of well blocks.
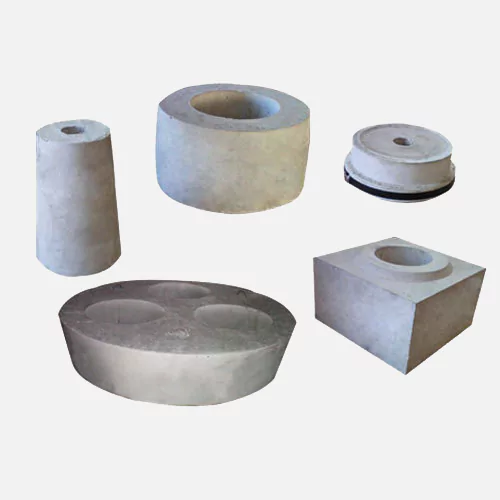
Well Block for Bottom Pouring Set Suppliers
Material Selection: Choose a suitable refractory material based on the intended application and the types of molten metals to be cast. Common refractory materials include high alumina, magnesia, zirconia, and combinations of these materials.
Material Preparation: Prepare the refractory material by mixing it with binders, additives, and sometimes fibers. This mixture enhances the material’s plasticity, workability, and thermal shock resistance.
Molding: The refractory material mixture is molded into the desired shape of the well block. This can be done using various techniques such as hand molding, pressing, slip casting, or extrusion.
Drying: The molded well block is dried slowly to remove moisture and binders. This step helps prevent cracking and warping during subsequent firing.
Firing (Sintering): The dried well block is fired in a kiln at high temperatures, often exceeding the operating temperature of the molten metal it will encounter during casting. This firing process helps the refractory material bond and harden, developing its structural integrity and resistance to thermal shock.
Advantages of Product
- Reduced Turbulence
- Temperature Maintenance
- Chemical Resistance
- Thermal Insulation
- Wear Resistance
- Improved Efficiency
- Enhanced Casting Quality
Features of Well Block :
- Temperature Control
- Chemical Resistance
- Thermal Insulation
- Wear Resistance
- Ease of Installation
- Reduced Metal Waste
Where It Is Used?
- Foundry Industry
- Automotive Manufacturing
- Energy Industry
- Heavy Machinery
- Cement Industry