Monoblock Stopper for Continuous Casting Manufacturers
One of the primary advantages of monoblock stoppers is their simplicity and ease of use in automated production lines. Their single-piece construction eliminates the need for assembly, reducing the risk of defects and ensuring consistent quality.
These stoppers are also favored for their excellent sealing properties, which help to maintain the freshness, potency, and integrity of the products they protect. Whether sealing pharmaceutical vials, beverage bottles, or other containers, monoblock stoppers play a crucial role in ensuring product safety and extending shelf life.
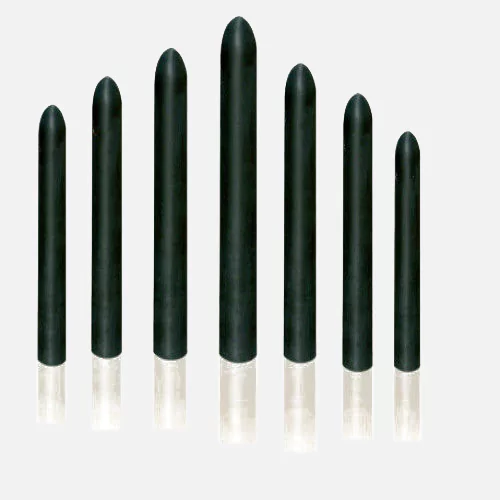
Monoblock Stopper for Continuous Casting Suppliers
The process begins with selecting the appropriate material for the monoblock stopper. Common materials include rubber (such as natural rubber or synthetic rubber) and silicone. The chosen material should have the right balance of flexibility, durability, and chemical resistance to suit the intended application.
The selected material is processed to create a workable form. This might involve mixing various compounds, additives, and colorants, if needed, to achieve the desired properties and appearance of the stopper.
Molding is a critical step in creating the monoblock stopper. There are different molding methods, such as injection molding or compression molding, that can be used depending on the material and the desired stopper design. During this step, the material is heated and injected or pressed into a mold cavity that matches the shape and dimensions of the stopper.
Advantages Of Our Products :
- Reduced Contamination Risk
- Visual Appeal
- Environmental Benefits
- Simplicity and Consistency
- Airtight Sealing
Where It Is Used?
- Household Chemicals
- Household Products
- Wine and Spirits
- Food Industry
- Cosmetics and Personal Care
- Beverage Industry
- Pharmaceutical Industry