Bottom Pouring Set Manufacturers in India
A bottom pouring set is a set of refractory bricks and shapes used to pour molten metal into an ingot mold from the bottom. It is typically made of fire clay or other refractory materials that can withstand high temperatures. The set includes a bottom plate, runner bricks, and riser bricks.
The bottom plate is placed on the bottom of the ingot mold and the runner bricks are used to direct the molten metal into the mold. The riser bricks are used to vent the air and gases from the mold.Bottom pouring is a common method for casting ingots in the steel industry. It has several advantages over other casting methods, such as top pouring and side pouring.
Jindal Refractories is the best Bottom Pouring Set Manufacturer in Wankaner, Gujarat and in all over the India.
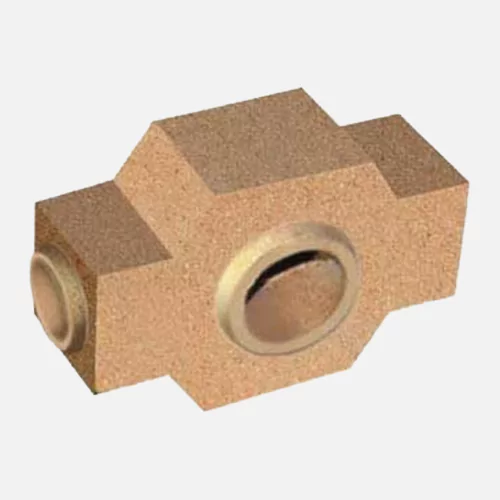
Bottom Pouring Set Suppliers in India
The manufacturing process of a bottom pouring set involves several steps to create the specialized equipment used for controlled pouring of molten metal. Here’s an overview of the typical manufacturing process for a bottom pouring set:
- The process begins with the design and engineering phase, where experts create detailed drawings and specifications for the bottom pouring ladle and its components. This includes the ladle body, stopper mechanism, nozzle, sprue, and any other relevant features.
- The choice of materials is crucial for a bottom pouring set’s performance under high temperatures and exposure to molten metal. Commonly used materials include refractory materials, heat-resistant alloys, and ceramics.
- Depending on the complexity of the ladle design, patterns and cores may be created. Patterns are replicas of the final ladle shape and are used to create molds. Cores are inserts placed in the mold to form internal features. For more intricate designs, patterns and cores can aid in achieving the desired ladle shape and internal passages.
- Molds are created using various techniques such as sand casting, investment casting, or die casting. The chosen method depends on the ladle’s design, size, and material. The mold needs to accommodate the ladle’s shape and internal features accurately.
- The chosen material for the ladle is melted using appropriate melting equipment like induction furnaces or electric arc furnaces. Once the molten metal is ready, it’s poured into the prepared molds. Careful attention is paid to ensure that the material flows uniformly and fills all areas of the mold.
- The cast ladle is likely to have rough surfaces, and any necessary machining is performed to achieve the desired shape and surface finish. This may involve turning, milling, grinding, and other machining processes.
- The finished ladle undergoes rigorous quality control and testing to ensure it meets the required standards. This may involve dimensional checks, material testing, leak testing, and other relevant tests.
- Depending on the ladle’s material and intended use, a final protective coating or lining may be applied to enhance its resistance to high temperatures, chemical reactions, and wear.
- Once the ladle passes all quality checks, it is packaged and prepared for distribution to foundries and manufacturing facilities where it will be used for metal casting processes.
The manufacturing process can vary based on the specific requirements of the ladle’s design, the materials used, and the intended application. Additionally, specialized equipment and expertise are often required for the fabrication of bottom pouring sets due to the challenging conditions they will be exposed to during metal casting operations.
Advantages of Bottom Pouring Set
- Improved quality of ingots
- Improved safety
- Reduced environmental impact
- Reduced Oxidation
- Minimized Turbulence
Where you can use Bottom Pouring Set
Bottom pouring sets are commonly used in various metal casting processes where precise control over the pouring of molten metal is essential for achieving high-quality castings.
- Iron and Steel Foundries
- Non-Ferrous Metal Casting
- Automotive Industry
- Energy Sector
- Custom Manufacturing